MEASUREMENT SYSTEMS |
Model Wind Turbine Test Rig
Specifications:
- 1 m to 1.4 m diameter rotors (adjustable pitch angles)
- Ability of air injection from hub to the channels in blade roots to investigate active flow control for various applications
- Driven by 1.5 KW Panasonic Servo Motor
- Equipped with HBM T20WN/5 Nm torque transducer
- Equipped with a 6-axis ATI Force/Torque transducer
Applications:
- Performance measurements studies
- Flow field measurements studies
- Active flow control studies
- Passive flow control studies
|
|
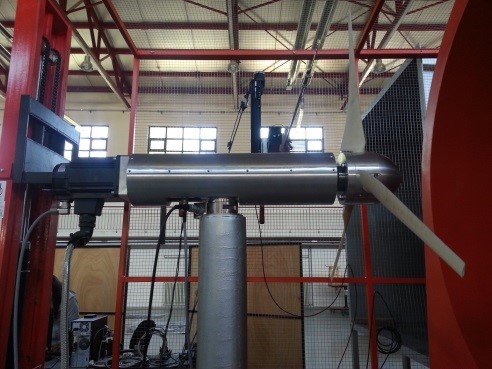
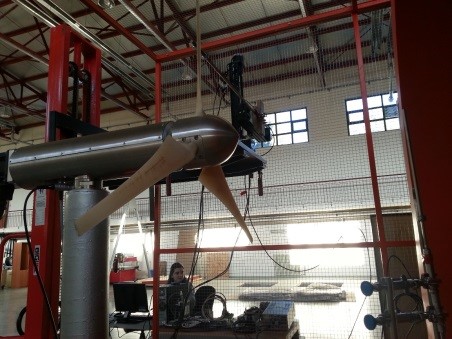
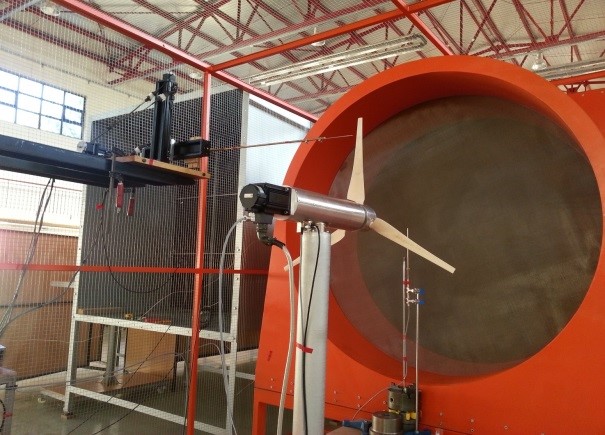
|
High Precision Force/Moment Balance
Specifications:
- Load balance system equipped with 6-axis ATI Force/Torque transducers
- Equipped with a stepper angle motor for angle of attack adjustment
Applications:
- Aerodynamic characteristics measurements of wing and bridge models in wind tunnels
|
|
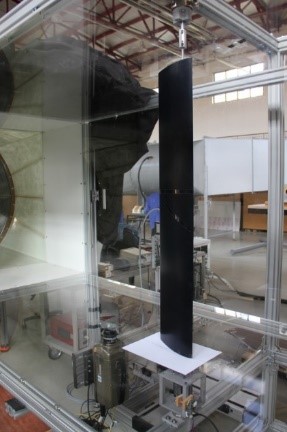 |
Particle Image Velocimetry
Specifications:
- TSI Incorporated
- Two Dimensional, Stereoscopic, Time-Resolved, Particle Image Velocimetry System
- Litron LDY304 series diode pumped Q-switched Nd: YLF high repetition rate (0.2-20 kHz) laser. The laser is a dual power, dual cavity with output energy at 1 kHz at 527 nm up to 30 mJ per laser head per pulse
- Two 12-bit high speed (Phantom V640) digital camera with a maximum resolution of 2560x1600 pixels at a frequency of 1.5 kHz (4 megapixel at full resolution) and 16 GB of internal memory buffer
- A Model 610036 LASER PULSE Synchronizer
- A 3-Axis ISEL heavy duty traverse system utilized for capturing image data at multiple planes in a flow.
- A six-jet oil droplet generator that utilizes a Laskin nozzle to generate droplets of 1 µm in diameter, used for flow seeding. Pressurized air atomizes oil in the generator reservoir to produce the droplets. These generators are best used with olive oil.
- INSIGHT 4G Acquisition Data System Software
- LASER PULSE Light Arm
- Various Light Sheet Optics. Various camera lenses and filters
- Breadboard, Laser safety Glasses
|
|
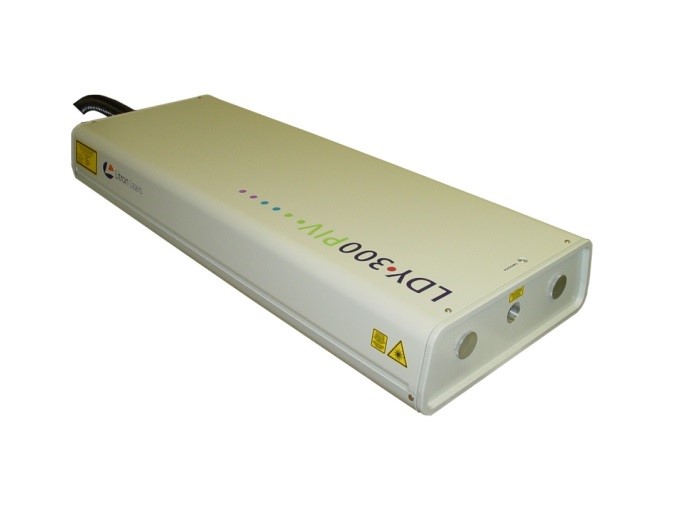
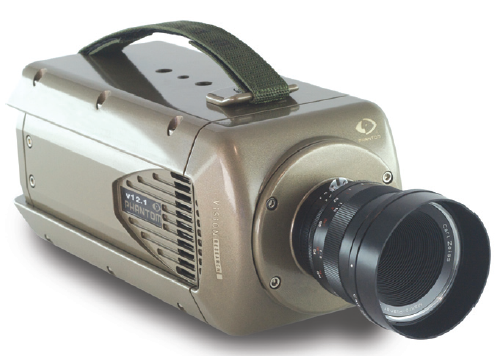
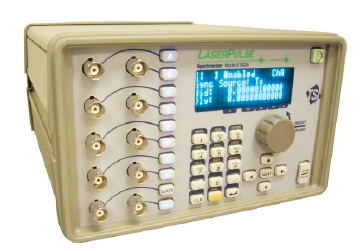
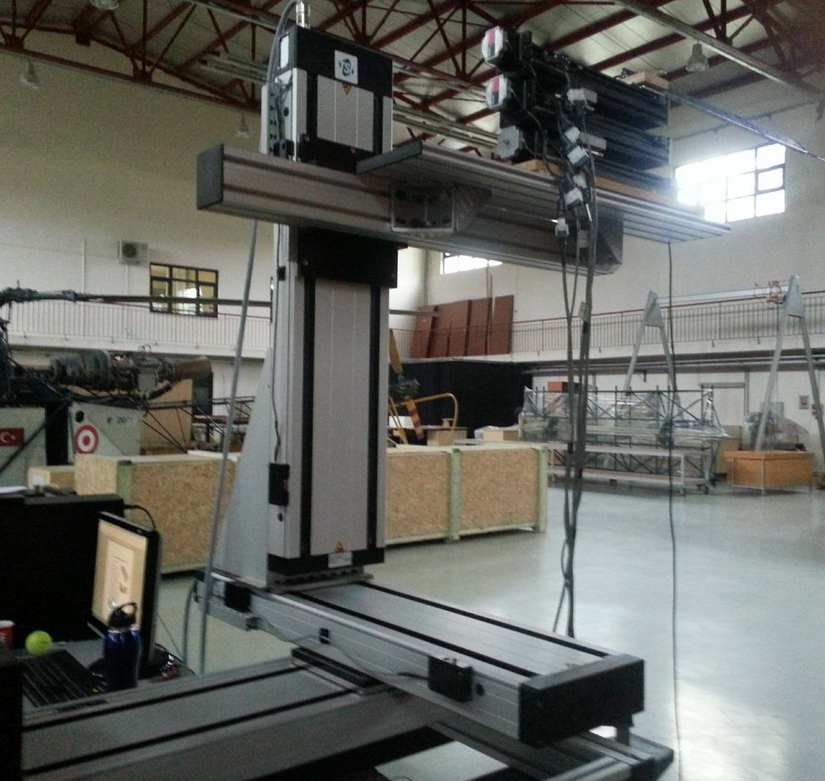
|
Pressure Measurement
Specifications:
- 128-channel ESP pressure scanner units
- DTC Initium DAQ pressure measurement system
- 16-channel DSA pressure Scanner from Scanivalve Corp
Applications:
- 5-hole pressure probe
- Pitot-static pressure probes
- Kiel probe
- Surface pressure measurements on wings
|
|
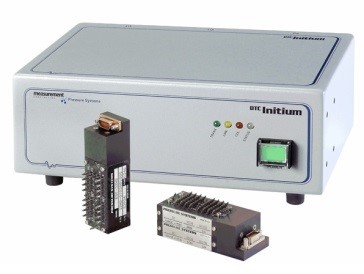
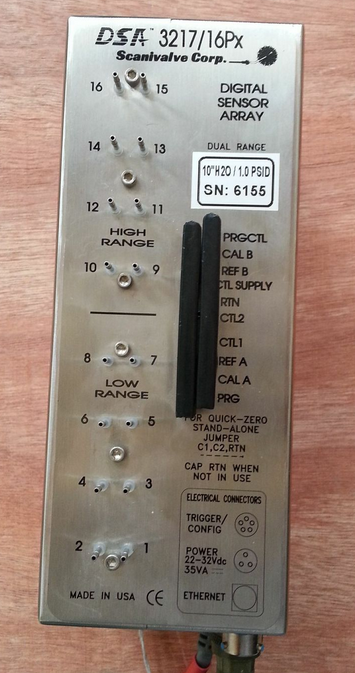
|
Data Acquisition System
Specifications:
- NI Compact DAQ -9172 8 slot USB Chassis
- 2 x 32-channel NI-9205 analog input module
- 8-channel NI-9472 24 V Sourcing Digital Output
- 4-channel NI-9211 Thermocouple analog input module
- NI Compact RIO-9076 4 slot Ethernet Chassis
- NI-9512 1 Axis Stepper Drive Interface Module
- LABVIEW programing software
Applications:
- Constant Temperature Anemometry (CTA) Measurements
- Pressure Measurements
- Motion Control Measurements
|
|
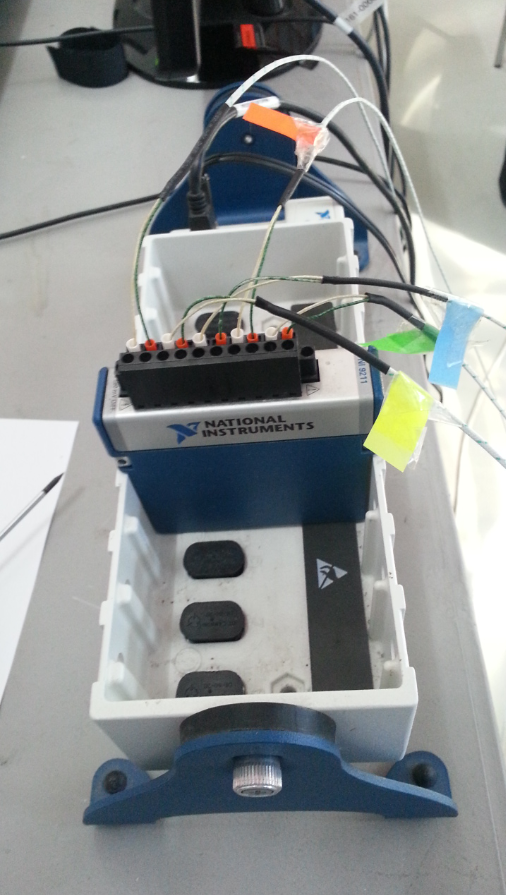
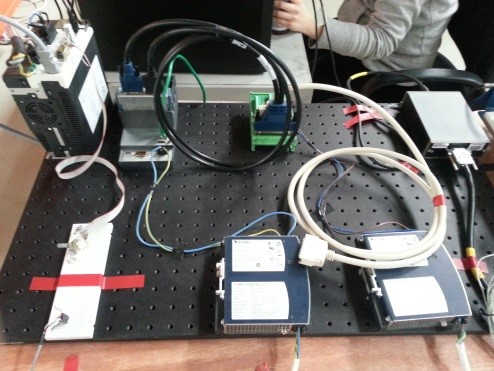
|